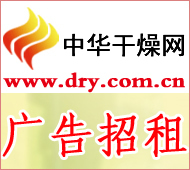
China Drying Network News In response to the widespread corrosion and corrosion problems of coal chemical installations in the operation of equipment and pipelines, a few days ago Sinopec organized coal chemical companies, engineering companies and related scientific research and testing organizations, held a seminar on the selection of coal chemical plant design guidelines. , And decided by the Ningbo Engineering Company, Luoyang Engineering Company, Sinopec Engineering Construction Company to take the lead in the preparation of the Sinopec coal chemical plant design selection guidelines. The industry believes that the current selection of coal chemical plant equipment does not have a unified standard, edge design, construction, and groping are common. The preparation of the guidelines for the design and selection of materials for the Sinopec coal chemical plant will have implications for the entire coal chemical industry. Only if the material is safe, economical, and reasonable, can we ensure intrinsic safety from the source and achieve long-term stable operation of coal chemical equipment.
Coal gasification is the leader of coal chemical industry. The compounds containing sulfur, chlorine and other elements as well as the water-soluble substances produced in coal gasification are strongly corrosive to metals, causing serious damage to the gasification equipment and subsequent systems and affecting the long-term stable operation of the system. With the prolonged operation of the equipment, various coal chemical companies have worn out or corroded to varying degrees, and leakage of equipment and pipelines has become an important cause of system shutdown. In 2011, a coal chemical company in Yunnan caused the system to stop for 2 times due to the corrosion and leakage of the syngas system pipeline. Due to defects in the original design and improper selection of some process pipelines, there was a lot of bottlenecks in the operation of a methanol plant in a coal chemical enterprise in Henan. In order to promote the stable, long-term, and full-scale operation of the device, the company invested 100 million yuan in special funds to implement major technological transformation of the original device.
The erosion and corrosion of equipment, valves, and pipelines have become a fundamental problem that affects the long-term stable operation of the equipment. Xiong Tongguo, a senior engineer of Baotou Coal Chemical Company of China Shenhua Coal Chemicals Co., Ltd., said that everything from equipment and pipelines to instruments and valves Choose the right material to improve corrosion resistance. The influence of chloride ion corrosion on the selection of gasification system is all-round, especially when the coal-water slurry gasification is used as the source of the process, the condensate is used as the main washing water for the carbonization tower of the gasifier, and then heated with the crude gas. The back-conversion device can easily cause the enrichment of sulfur ions and chloride ions. The Yellow River water is commonly used in the northwest region and has a high chloride ion content. A domestic company uses 304-type steel as a conversion process gas and condensate line. It soon discovered that cracks appeared in the elbow weld at the non-destructive testing process. After driving for more than three months, a large area of ​​pipeline cracks appeared in the conversion system. Affects production and becomes a great safety hazard.
Xiong Tongguo believes that under conditions of economic permissibility, dual-phase steels or high-alloy stainless steels may be used for equipment and pipelines with severe chloride ion corrosion. In order to reduce costs, it may also be considered to add suitable linings inside the equipment or pipelines in order to improve the resistance to chloride ion corrosion of equipment and pipelines. For slag pools and clarifiers where the concentration of chloride ions is high, because the medium they pass through contains a large amount of ash, the wear on the equipment and pipes is very large. Therefore, it is necessary to prevent corrosion and prevent wear. Consider the equipment. The shell is made of carbon steel and internally lined with wear-resistant, chloride-resistant, corrosion-resistant liners to save costs.
It is understood that as the coal chemical industry becomes more and more large-scale, coal chemical equipment is also becoming large-scale, and the steel plates and composite plates used are getting thicker and thicker. The requirements for inspection and testing of materials are higher, and high standards for inspection and testing are directly Determine the safety of the material. At present, the newly implemented "Regulations for the Supervision of Safety Technologies for Stationary Pressure Vessels" relaxes the requirements for re-inspection of the pressure-receiving element materials. At the same time, coal chemical companies and equipment manufacturers also relax the inspection of material properties. Gao Gong Song Wenxuan of Shanghai Coking Co., Ltd. believes that relaxing the requirements for incoming materials of pressed parts materials is suitable for the mature steel sheet, but it will be applied to domestically produced Cr-Mo steels, low-temperature steels and high-strength steels ≥60mm thick plates. Said that it is at the stage of development of localization, performance is not yet stable, it is necessary to re-inspect the factory.
It is understood that several domestic large-scale steel plants and equipment manufacturing plants have experienced unqualified re-inspection of low-temperature thick plate materials, and imported steel plates have also undergone retest in the equipment manufacturing process. At present, due to the re-inspection of heavy plate materials, there is no standard specification, the design documents of various engineering companies and design institutes are uneven, and the retesting inspection ratio regulations are also arbitrarily large.
Zhao Qingwan, chief engineer of the Chemical Industry Equipment Quality Supervision and Inspection Center, pointed out that in order to ensure the safe operation of the equipment plant manager in the future, the 18-hour maximum simulated heat treatment mechanical properties must be written into the material and equipment procurement contract. Moreover, with the increasing thickness of stainless steel clad materials, some companies have now increased their requirements and require 24 to 26 hours maximum mechanical properties under simulated heat treatment.
In addition, due to the fact that the intergranular corrosion is not easy to inspect and cause sudden destruction of equipment , it is a form of great harm in corrosion damage. As the equipment becomes larger and the composite board becomes thicker, the post-weld heat treatment time becomes longer. Experts suggest that in the technical requirements for the supply of stainless steel clad shell materials, intergranular corrosion tests must also be conducted under heat treatment conditions.
Place the meat on special trays, plate paper or film for skin packaging, a three-dimensional packaging effect is formed, which improves the shelf level and achieves the purpose of oxygen insulation, freshness, moisture, poison, rust, corrosion, pollution, etc., which is effective Extended shelf life is convenient for storage and transportation.
The skinned vacuum packaging machine is a new type of product packaging technology. The skinned packaging can extend the shelf life of the product, have a strong three-dimensional view, and is not easy to pack. It can be widely used in hardware tools, auto parts, medical equipment, electrical and electronic components, and toys. , Stationery, knives, tableware and crafts, etc. Especially suitable for packaging of various seafood such as sea cucumber, abalone, lobster, etc.
The skin packaging is formed by vacuum suction according to the shape of the product and pasted on the cardboard (or bubble cloth, etc.). The transparent skin film is heated and softened and then covered on the product.
The vacuum pump of this equipment adopts the BUSCH100 vacuum pump imported from Germany from Puxu Company. The frame is made of stainless steel. The upper cover is made of 6mm thick 304 stainless steel, and the lower cover is made of integral cast aluminum alloy. The air cylinder uses Airtac thin cylinders, the electrical appliances use Siemens or Schneider AC contactors, Delta microcomputer control, Delta interface display adjustment, German Turck non-contact induction switch, Airtac pneumatic components.
Vacuum Packaging Machine,Vacuum Skin Packaging Machine,Vsp Packaging Machine,Vacuum Pack Machine
Henan Gems Machinery Co.,Ltd , https://www.gemsmachines.com