Preventive Maintenance: A Guide
Preventive maintenance refers to a series of routine procedures designed to minimize equipment failure and unplanned downtime. By proactively addressing potential issues, organizations can maintain operational efficiency and reduce costs associated with unexpected breakdowns.
These procedures encompass tasks like regular inspections, lubrication, and adjustments. Beyond manual upkeep, preventive maintenance also involves strategic planning, scheduling, and thorough documentation of past maintenance activities. Companies employing heavy machinery often adopt these practices to ensure consistent functionality and optimal productivity.
Industries such as oil and gas, manufacturing, and mining rely heavily on preventive maintenance to sustain operations and comply with regulatory standards.
What Is Preventive Maintenance?
Preventive maintenance involves scheduled routines carried out to reduce the risk of equipment failure. This includes activities like inspections, cleanings, part replacements, and minor repairs. The primary goal is to uphold the manufacturer's design intent while minimizing workplace risks, unplanned downtime, and repair expenses.
The Elios 3 inspecting a water management system
Why Is Preventive Maintenance Important?
Implementing preventive maintenance offers numerous advantages that enhance organizational efficiency and financial stability. Key benefits include reduced equipment downtime, enhanced worker safety, and compliance with industry regulations.
Compared to reactive maintenance, which addresses failures only after they occur, preventive maintenance is far more cost-effective. Reactive maintenance often leads to higher expenses and prolonged downtime. Conducting regular checks prevents equipment from failing unexpectedly, enabling companies to adopt a proactive approach.
Moreover, preventive maintenance plays a crucial role in budget planning. By integrating these strategies into long-term financial frameworks, businesses can allocate resources more effectively and align their efforts with future objectives.
Advantages of Preventive Maintenance
Preventive maintenance aims to preemptively address potential issues before they escalate. Here’s a closer look at why this practice is essential:
Minimizes Downtime
Well-maintained equipment operates smoothly, reducing the likelihood of unplanned disruptions. According to research by Aberdeen Strategy and Research, unexpected downtime can cost businesses an average of $260,000 per hour in lost revenue. Furthermore, such interruptions can harm client relationships, leading to additional financial losses.
Proper preventive maintenance ensures that downtime is predictable and manageable. Scheduled maintenance minimizes surprises and allows teams to prepare accordingly.
Extends Equipment Lifespan
Regular servicing extends the operational life of machinery. Assets that undergo routine inspections and upkeep last longer, reducing waste and maximizing return on investment. By delaying the need for new purchases, companies can allocate funds to other critical areas.
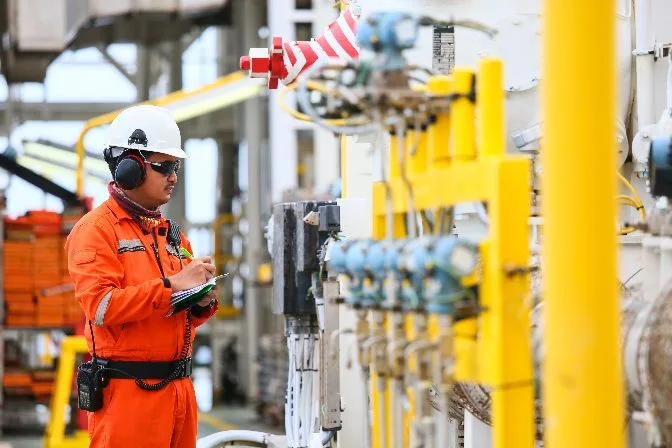
An inspector recording the operation of oil and gas processes
Enhances Worker Safety
Operational assets functioning correctly contribute to a safer work environment. Preventive maintenance mitigates risks associated with equipment failure, preventing accidents and protecting employees. Regular servicing identifies and resolves hazards before they become severe, reducing the frequency of workplace injuries.
Additionally, preventive maintenance poses fewer dangers than reactive approaches like run-to-failure (RTF) maintenance. Addressing issues proactively safeguards workers and avoids exposing them to unnecessary risks.
Ensures Regulatory Compliance
Many industries enforce strict guidelines for conducting preventive maintenance. Failure to adhere to these standards can result in fines or penalties. Implementing a consistent maintenance schedule guarantees compliance and shields organizations from legal repercussions.
Limitations of Preventive Maintenance
While preventive maintenance is highly beneficial, it requires integration within a broader maintenance strategy centered on safety and failure prevention. Despite some limitations, it remains one of the most effective methods for extending asset longevity.
Effectiveness
Although preventive maintenance significantly reduces the probability of equipment failure, it cannot eliminate all risks entirely. Accidents, natural disasters, and unforeseen circumstances remain challenging to anticipate fully.
Technological Challenges
Some assets feature sensors and gauges that facilitate early detection of issues. However, others rely solely on fixed schedules. Predictive maintenance, which uses advanced analytics to forecast failures, surpasses traditional preventive techniques in accuracy.
Initial Costs
While less expensive than reactive or predictive maintenance, preventive maintenance incurs upfront expenses. Smaller enterprises with constrained budgets may struggle to finance necessary procedures, including planned downtimes.
Changing a car filter
Time Constraints
Maintenance tasks demand time and resources. Occasionally, equipment must be shut down for inspection, impacting production goals. Scheduling preventive maintenance becomes particularly challenging in resource-limited environments.
Staff Requirements
Effective preventive maintenance necessitates additional personnel or extended working hours. Thorough inspections and upkeep require significant effort, straining existing resources.
Over-Maintenance Risks
Allocating excessive resources toward unnecessary precautions can lead to inefficiencies. A well-adjusted preventive maintenance plan should incorporate historical data while maintaining a consistent schedule.
Types of Preventive Maintenance
Preventive maintenance can be categorized into three main types:
- Time-Based Maintenance
- Usage-Based Maintenance
- Condition-Based Maintenance
Time-Based Maintenance
Also known as calendar-based maintenance, this approach involves performing tasks at fixed intervals. For instance, replacing air filters every three months is a classic example of time-based maintenance. Manufacturers often specify these intervals, which can range from weekly to annually.
Historical records play a vital role in identifying equipment requiring special attention. However, time-based practices occasionally lead to over-maintenance. A filter replaced every three months might suffice for high-traffic areas but prove wasteful in low-usage settings.
Cleaning a condenser tube from a chiller
Usage-Based Maintenance
This type focuses on tracking usage metrics to trigger maintenance activities. Instead of relying on timeframes, usage-based maintenance considers factors like cycle counts, mileage, operating hours, or runtime. Tire rotations and transmission checks are prime examples.
By aligning maintenance efforts with actual usage levels, this method prevents over-maintenance and optimizes resource allocation.
Condition-Based Maintenance
Condition-based maintenance monitors an asset’s performance in real-time. Inspectors analyze data to determine when maintenance is required. Proper implementation ensures timely interventions, restoring reliability.
Common indicators include unusual sounds, temperature fluctuations, vibrations, or visible wear. These signals prompt inspections and subsequent maintenance actions.
Types of Preventive Maintenance Tasks
Each preventive maintenance category comprises specific tasks classified by priority. These tasks may be time-based, usage-based, condition-based, or hybrid. Examples include:
- Mandatory Tasks: Essential activities requiring immediate execution to avoid failure. Examples include cooling equipment components or emptying waste containers.
- Non-Mandatory Tasks: Important but flexible tasks that can be postponed without immediate consequences. Surface inspections fall into this category.
- Pyramiding Tasks: Overlapping tasks caused by missed deadlines. Performers must track overdue responsibilities to avoid cascading delays.
- Inspection Tasks: Condition-based tasks requiring prior inspections to identify issues. Maintenance follows only after inspections confirm problems.
- Task-Oriented Tasks: Combining inspections with maintenance to streamline processes and reduce labor costs.
What Is a Preventive Maintenance Checklist?
A preventive maintenance checklist outlines tasks, targets, and procedures integral to a comprehensive maintenance plan. These lists are collaboratively developed with maintenance managers, field workers, contractors, and regulators.
Many organizations leverage preventive maintenance software to create, monitor, and document these checklists efficiently.
Benefits of a Preventive Maintenance Checklist
Like all preventive maintenance initiatives, checklists strive to improve efficiency, minimize downtime, and enhance worker safety. Additional advantages include:
- Reduced human error
- Improved diagnostics
- Faster inspections
- Targeted training programs
- Efficient maintenance planning
- Consistent workplace practices
Preventive Maintenance Checklist Examples
Checklists vary across industries and organizations but share similar purposes. Below are examples from three distinct fields:
Building Interior Preventive Maintenance Checklist
- Inspect for visible signs of deterioration
- Check for leaks
- Assess electrical, slip/trip hazards
- Inspect toilet and shower conditions
- Test smoke and CO detectors
- Verify fire alarm systems
- Inspect fire extinguishers
- Ensure exit routes are clear
- Check door locks and closures
- Mark workspaces clearly
- Monitor garbage storage
- Look for pest activity
- Inspect cart casters
- Secure and label shelves
- Check electrical cover plate integrity
- Confirm timer and photocell functionality
Network and Data Systems Preventive Maintenance Checklist
- Review network security protocols
- Identify emerging network threats
- Ensure employee adherence to security practices
- Rotate Wi-Fi and network passwords semiannually
Semi-Truck Preventive Maintenance Checklist
- Conduct standard safety checks
- Lubricate key components
- Inspect brakes
- Verify light functionality
- Check tire condition and inflation
- Top off fluids
- Adjust high-wear parts
Drones in Preventive Maintenance
Visual condition monitoring serves as a cornerstone of preventive maintenance. Among the most innovative solutions is the use of drones or unmanned aerial vehicles (UAVs).
Agile UAVs offer immense value in various maintenance contexts. They enable condition-based monitoring by capturing real-time imagery and data. Additionally, drones can autonomously execute certain time-based or usage-based tasks.
In some cases, drones allow inspections without halting production. At other times, they drastically reduce downtime by eliminating the need for scaffolding. The Elios 3 drone, equipped with LiDAR sensors, exemplifies this capability. Used by the City of Lausanne’s Water Department, it creates detailed asset maps, tracking wear and tear over time.
Drones not only reduce costs and speed up tasks but also keep inspectors safe by eliminating exposure to hazardous environments. With Flyability’s Elios drones, workers can conduct inspections remotely, avoiding risks posed by malfunctioning machinery.
An Elios 3 drone performing a visual inspection
U-Type cover plates are used for grate coolers, which are installed in cement kiln to cool the cement clinker.
U-Shaped Cover Plates,U Shaped Metal Plate,U Shaped Steel Plate,High Nickel Alloy U-Shaped Cover Plates
Jilin Huanyu New Materials Manufacturing Co., Ltd , https://www.huanyufoundry.com