In January 2007, the new catalyst developed by Qingdao Allied Letters was successfully applied in the world's first pulverized coal gasification low-water/sulfur-tolerant conversion ammonia plant in Liuzhou Chemical Industry Co., Ltd., filling up the sulfur-tolerant shift catalyst in “pulverized coal gasificationâ€. The international gap in the application of low water/gas shifting process has opened up a new process approach for smooth production, energy saving and environmental protection for the production of synthesis gas using pulverized coal gasification.
In addition, in May 2006, the catalyst was successfully applied in the first high-pressure low-to-low ammonia plant in Tianji-Gaoping Zhonghua Coal Chemical Industry Co., Ltd., filling the entire low pressure at a pressure greater than 3.5 MPa. "Change" technology technology catalyst application of the domestic blank. Atmospheric gasification technology is a traditional gasification technology adopted by small and medium-sized enterprises in China. The key to matching the high-pressure and sulfur-resistant conversion technology in the subsequent sections is the application of the catalyst. The successful application of the QDB series of catalysts has set a good example for domestic coal-based raw materials using atmospheric pressure gasification to support high-pressure and sulfur-tolerant plants.
In October 2005, the catalyst was successfully applied in the first domestic high pressure partial depth methanol conversion plant of Yantai Guotai Chemical Co., Ltd. Yankuang Guotai Chemical Co., Ltd. has an annual output of 240,000 tons of methanol plant and is the first domestic methanol plant to adopt domestic independent innovation and gasification technology. At the beginning of the drive, due to the frequent fluctuations in the process conditions of the new gasification plant, the start-up and shutdown are more frequent. QDB series catalysts have experienced good performance and can meet the requirement of 30% increase in load when they have experienced frequent open and shutdown tests, and have been well received by users.
By April 2008, QDB catalysts had been used for more than six years in the ramp-up process of the Yanzhou-Minnan Lunan Fertilizer Plant, creating the first national record of a mid-varying furnace operating time of more than 6 years in an all-low-change process. For more than 6 years, reducing the number of opening and stopping at least 10 times has not only improved the activity and activity stability of the catalyst under low-sulfur conditions, but also completely solved the problem of poor catalyst strength stability and powdering ability, and achieved a remarkable economy. benefit.
Recently, they signed an application agreement with Anhui Linquan for the first set of sulfur-tolerant conversion catalysts for use in aerospace gasification and are expected to be put into operation in the second half of this year. This indicates that China's self-developed gasification technology and sulfur-tolerant conversion technology will replace foreign products, breaking the monopoly gasification of foreign companies and the high concentration of sulfur-tolerant shift catalyst technology.
Fly ash block manufacturing plant is a AAC block manufacturing process with fly ash as the main material, as you may know that the fly ash is an industrial waste, which can be derived from power station and cement making plant. And as it`s ground before burning, so it`s not necessary to use Ball Mill to grind it again, and this is the main difference between the two processes. However the lime still need to be ground, after materials batching and mixing, the slurry will be poured into a mould, where the green cake may go through several different processes, such as per-curing, cutting process, curing inside the autoclaves, after curing, the finished AAC is produced, and will be transported to clients after packing.
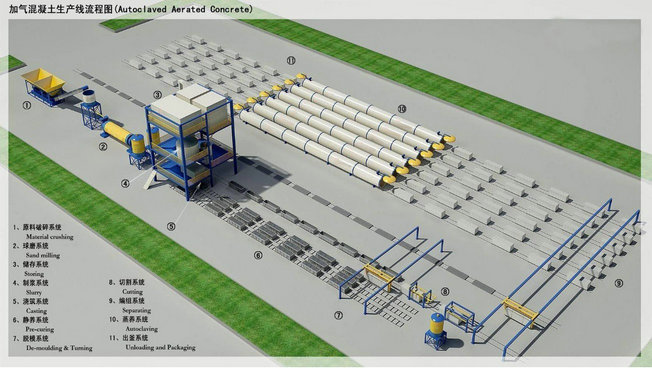
Fly Ash Aac Production Plant,Aac Plant Machinery,Aac Manufacturing Plant,Aac Block Making Plant
Henan Mingyuan Heavy Industrial Machinery Company Co., LTD. , https://www.heavyequipmentchina.com