Wrought steel and cast steel are often confused by both consumers and manufacturers, as they both fall under the broader category of iron-based metals. However, these two materials are fundamentally different in terms of composition, manufacturing process, and properties. Understanding their distinctions is crucial when choosing the right material for a specific application.
Wrought steel is typically produced by heating the metal and then shaping it using mechanical tools and processes like rolling, forging, or extrusion. This method allows for greater control over the material's structure, resulting in a more uniform and ductile product. On the other hand, cast steel is created by melting the metal and pouring it into a mold, where it solidifies into the desired shape. The casting process is ideal for producing complex forms that would be difficult to achieve through traditional forming methods.
One key difference between the two is the carbon content. Wrought steel usually contains less carbon than cast steel, which makes it more malleable and easier to work with. This lower carbon content also contributes to its superior weldability and flexibility, making it suitable for applications requiring high strength and formability. In contrast, cast steel has a higher carbon content, giving it increased hardness and wear resistance but reducing its ability to be easily shaped or welded.
Wrought steel offers several advantages, including excellent ductility, good welding properties, and high tensile strength. It is commonly used in structural components, machinery parts, and architectural elements where flexibility and durability are essential. Its ability to be reheated and reshaped makes it highly versatile for various fabrication needs.
Cast steel, on the other hand, excels in applications where high compressive strength and wear resistance are required. It is widely used in heavy machinery, engine blocks, and industrial equipment. While it is less flexible than wrought steel, its ability to withstand extreme conditions makes it an ideal choice for demanding environments.
Table of contents
- Difference between wrought steel and cast steel
- Heat Treatment of cast steel
- Advantages and Disadvantages of cast iron steel
- Advantages of wrought iron
- Puddling process vs Metal Casting process
- Types of cast iron
- Properties of 4140 cast steel
- Chemical composition of Cast iron
- Cast Iron mechanical properties
- AISI 4140 Heat Treatment
- Wrought Iron chemical composition
- Wrought Steel mechanical properties
- Inspection and Testing of Cast steel
- Manufacturing process of 4340 steel casting
- Cast steel valves temperature range
- Difference between Wrought Iron and Steel
- Surface finish of Cast iron parts
Difference between wrought steel and cast steel
Wrought Iron | Cast Iron |
---|---|
It is iron that has been heated and then worked with tools. | It is iron that has been melted, poured into a mold, and allowed to solidify |
It is brittle | It is ductile |
Higher tensile strength | Lower tensile strength compared to Wrought Iron |
Low melting point | High melting point |
It is difficult to weld | It is easily welded |
Proper techniques for welding cast steel, explore 4140/4340 steel heat treatment and casting hardness
Heat Treatment of cast steel
- Annealing
- Precipitation Strengthening
- Tempering
- Case Hardening
- Normalising
- Quenching
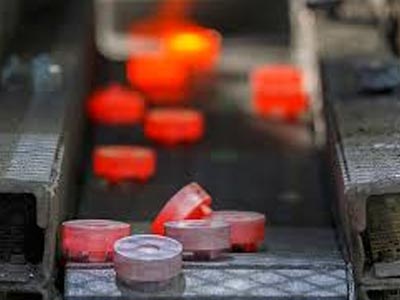
Explore the benefits of both cast and wrought steel products
Advantages and Disadvantages of cast iron steel
Advantages
- Cast iron has excellent fluidity after melting
- High Wear Resistance
- Excellent Machinability
- Compression Strength
- Low Cost
Disadvantages
- It is relatively brittle and may fracture
- Very easily gets rusted
- It is relatively heavy
Advantages of wrought iron
- Increased ductility
- Excellent weldability
- Easily forged
- High tensile & compressive strength
- Enhanced malleability
Compare the puddling process with the metal casting process
Puddling process vs Metal Casting process
The puddling process involves converting pig iron into wrought iron by heating and stirring it in a furnace without using charcoal. This was one of the earliest methods for producing wrought iron in large quantities. In contrast, metal casting involves melting metal and pouring it into a mold to create a specific shape. This technique is especially useful for creating intricate designs that are challenging to produce using other methods.
Types of cast iron
Gray Cast Iron
Ductile Cast Iron
White Cast Iron
Malleable Cast Iron
Properties of 4140 cast steel
- Hardness
- Ductility
- Wear resistance
- Corrosion resistance
- Toughness
- Strength
- Machinability
- Weldability
- Low-temperature properties
- High-temperature properties
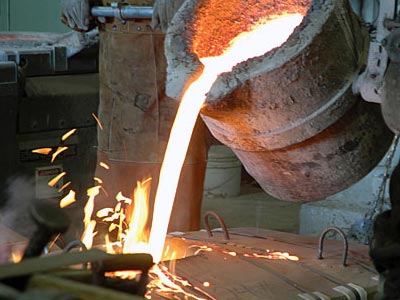
Explore types of cast steel materials, grades, composition, and density in kg/m³
Chemical composition of Cast iron
ASTM | Chemical Requirements | ||||
---|---|---|---|---|---|
STEEL GRADE | Carbon | Manganese | Silicon | Sulfur | Phosphorus |
Max % / Range | |||||
ASTM A27 / A27M | |||||
Grade N-1 | 0.25 | 0.75 | 0.80 | 0.06 | 0.05 |
Grade N-2 | 0.35 | 0.60 | 0.80 | 0.06 | 0.05 |
Grade U60-30 | 0.25 | 0.75 | 0.80 | 0.06 | 0.05 |
Grade 60-30 | 0.30 | 0.60 | 0.80 | 0.06 | 0.05 |
Grade 65-35 | 0.30 | 0.70 | 0.80 | 0.06 | 0.05 |
Grade 70-36 | 0.35 | 0.70 | 0.80 | 0.06 | 0.05 |
Grade 70-40 | 0.25 | 1.20 | 0.80 | 0.06 | 0.05 |
ASTM A148 / A148M | |||||
Grade 80-40 | N/A | N/A | N/A | 0.06 | 0.05 |
Grade 80-50 | N/A | N/A | N/A | 0.06 | 0.05 |
Grade 90-60 | N/A | N/A | N/A | 0.06 | 0.05 |
ASTM A216 / A216M | |||||
Grade WCA | 0.25 | 0.70 | 0.60 | 0.045 | 0.04 |
Grade WCB | 0.30 | 1.00 | 0.60 | 0.045 | 0.04 |
Grade WCC | 0.25 | 1.20 | 0.60 | 0.045 | 0.04 |
Cast Iron mechanical properties
ASTM | Mechanical Properties | |||
---|---|---|---|---|
STEEL GRADE | Tensile Strength | Yield Point | Elongation in 2 in. | Reduction of Area |
Min. ksi [Mpa] / Range | Min. % | |||
ASTM A27 / A27M | ||||
Grade U60-30 | 60 [415] | 30 [205] | 22 | 30 |
Grade 60-30 | 60 [415] | 30 [205] | 24 | 35 |
Grade 65-35 | 65 [450] | 35 [240] | 24 | 35 |
Grade 70-36 | 70 [485] | 36 [250] | 22 | 30 |
Grade 70-40 | 70 [485] | 40 [275] | 22 | 30 |
ASTM A148 / A148M | ||||
Grade 80-40 | 80 [550] | 40 [275] | 18 | 30 |
Grade 80-50 | 80 [550] | 50 [345] | 22 | 35 |
Grade 90-60 | 90 [620] | 60 [415] | 20 | 40 |
ASTM A216 / A216M | ||||
Grade WCA | 60-85 [415-585] | 30 [205] | 24 | 35 |
Grade WCB | 70-95 [485-655] | 36 [250] | 22 | 35 |
Grade WCC | 70-95 [485-655] | 40 [275] | 22 | 35 |
AISI 4140 Heat Treatment
Soft annealing °C | Cooling | Hardness HB |
---|---|---|
650-700 | slowly | max. 280 |
Stress-relief annealing °C | Cooling |
---|---|
630 – 650 | Furnace |
1st pre-heating °C | 2nd and 3rd | Hardening °C | Quenching | Tempering °C | Hardness after Tempering HRC |
---|---|---|---|---|---|
up to approx. 400 in an air-circulating furnace | 780 and 1000 | 1190 – 1230 | Saltbath, at least 520 °C Oil ,Air | at least twice 530-560 | 64 – 66 |
Wrought Iron chemical composition
Element | Iron, Fe | Carbon, C | Phosphorus, P | Silicon, Si | Sulfur, S | Manganese, Mn |
---|---|---|---|---|---|---|
Content (%) | 99-99.8 | 0.05-0.25 | 0.05-0.2 | 0.02-0.2 | 0.02-0.1 | 0.01-0.1 |
Wrought Steel mechanical properties
Properties | Imperial | Metric |
---|---|---|
Tensile strength | 34000-54000 psi | 234-372 MPa |
Modulus of elasticity | 28000 ksi | 193100 MPa |
Yield strength | 23000-32000 psi | 159-221 MPa |
Inspection and Testing of Cast steel
- Dimensional accuracy
- Surface finish condition
- Internal soundness
- Chemical analysis
- Heat analysis
- Tensile properties
- Impact properties
- Hardness
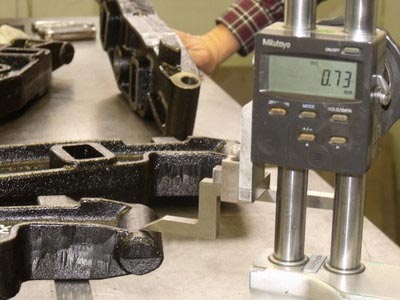
Manufacturing process of 4340 steel casting
- Furnace charging
- Melting
- Refining
- De-slagging
- Tapping (or tap out)
- Furnace turn-around
Learn about cast steel valves uses and temperature limits
Cast steel valves temperature range
Temperature range | -29°C to 425°C |
---|
Difference between Wrought Iron and Steel
Characteristics | Wrought Iron | Steel |
---|---|---|
Carbon content | 0.08% | 4% |
Tensile Strength | Very good tensile strength | Greater tensile strength |
Workmanship | Requires less workmanship. | Requires more craftsmanship than wrought iron |
Surface finish of Cast iron parts
- Shot Blasting
- Painting
- Powder Coating
- Electroplating
Hardware Slide Blister Packaging
We can produce the slide card blister packs according to your samples or design,the material can be PP,PET,PVC,PS.Our ability includes tooling making ,thermoforming ,vacuum forming .All in one place insure our most competitive price and guarantee quality!
Blister cards are a key component in many retail packages,such as plastic clamshell packaging and slide blister pack .You can put your brand name and company information on the cards,make your product more attractive and beautiful ,and it can also product your products during transportation .
The sliding blister packaging is great for display the products inside ,we can also customized the cavity shape according to your goods .If any question,feel free contact us !
Slide blister packaging ,transparent slide blister pack ,slide blister pack
Shenzhen Stardeal Industrial Co.,Ltd , https://www.plasticblisterpack.com