Wrought steel and cast steel are often confused by consumers and manufacturers due to their similar names. However, they are fundamentally different materials with distinct properties and applications.
Wrought steel is typically heated and then shaped using tools and machinery, while cast steel is melted and poured into molds where it solidifies. The names of these steels also reflect their manufacturing processes—wrought steel means "worked steel," and cast steel refers to the casting process used in its production.
Wrought steel is known for its high ductility, allowing it to be reheated and reshaped multiple times. One of its key advantages is that its strength increases when it's worked. It contains less carbon than cast iron, making it more malleable and easier to work with. Here are some of its main benefits:
- Excellent welding properties, making it easy to shape according to specific needs.
- High flexibility and ductility, ideal for applications requiring bendability or formability.
- Strong tensile strength, suitable for use in harsh environments.
- Easy to forge, enabling the creation of complex shapes without significant difficulty.
Cast steel, on the other hand, has a higher carbon content (between 2.0% and 4.0%) and includes elements like manganese and silicon. It is produced by melting iron ore and combining it with scrap metals and alloys. The molten mixture is then poured into molds and allowed to cool and harden. Compared to wrought steel, cast steel is harder, more brittle, and less malleable.
It is widely used in the production of cookware, mechanical equipment, and construction materials. Its advantages include:
- High compressive strength, offering resistance to pressure.
- Good durability and toughness, which can be further improved through alloying and heat treatment.
- Excellent machinability, making it easy to cut, grind, and drill into desired shapes.
- High wear resistance, especially when enhanced with elements like chromium or molybdenum.
Table of contents
- Difference between wrought steel and cast steel
- Heat Treatment of cast steel
- Advantages and Disadvantages of cast iron steel
- Advantages of wrought iron
- Puddling process vs Metal Casting process
- Types of cast iron
- Properties of 4140 cast steel
- Chemical composition of Cast iron
- Cast Iron mechanical properties
- AISI 4140 Heat Treatment
- Wrought Iron chemical composition
- Wrought Steel mechanical properties
- Inspection and Testing of Cast steel
- Manufacturing process of 4340 steel casting
- Cast steel valves temperature range
- Difference between Wrought Iron and Steel
- Surface finish of Cast iron parts
Difference between wrought steel and cast steel
Wrought Iron | Cast Iron |
---|---|
It is iron that has been heated and then worked with tools. | It is iron that has been melted, poured into a mold, and allowed to solidify |
It is brittle | It is ductile |
Higher tensile strength | Lower tensile strength compared to Wrought Iron |
Low melting point | High melting point |
It is difficult to weld | It is easily welded |
Right technique for welding cast steel, check 4140/ 4340 Steel Heat Treatment and Casting hardness
Heat Treatment of cast steel
- Annealing
- Precipitation Strengthening
- Tempering
- Case Hardening
- Normalising
- Quenching
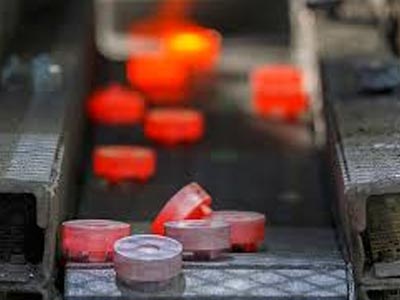
Refer advantages of Cast and Wrought Steel products
Advantages and Disadvantages of cast iron steel
Advantages
- Cast iron has excellent fluidity after melting
- High Wear Resistance
- Excellent Machinability
- Compression Strength
- Low Cost
Disadvantages
- It is relatively brittle and may fracture
- Very easily get rusted
- It is relatively heavy
Advantages of wrought iron
- Increased ductility
- Excellent weldability
- Easily forged
- High tensile & compressive strength
- Enhanced malleability
Check difference between puddling of cast iron and Metal Casting process
Puddling process vs Metal Casting process
The puddling process involves converting pig iron into wrought iron by heating and stirring it in a furnace without using charcoal. This was an early method for producing wrought iron in large quantities.
On the other hand, metal casting involves pouring molten metal into a mold, allowing it to solidify into the desired shape. This process is ideal for creating complex components that would be difficult or expensive to produce otherwise.
Types of cast iron
Gray Cast Iron
Ductile Cast Iron
White Cast Iron
Malleable Cast Iron
Properties of 4140 cast steel
- Hardness
- Ductility
- Wear resistance
- Corrosion resistance
- Toughness
- Strength
- Machinability
- Weldability
- Low-temperature properties
- High-temperature properties
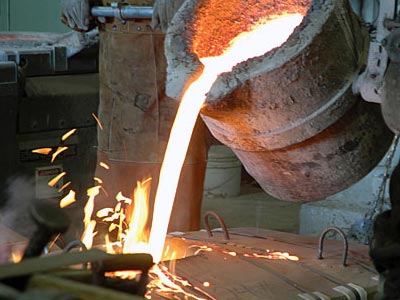
Types of Cast Steel material, check grades, composition, and density in kg/m3
Chemical composition of Cast iron
ASTM | Chemical Requirements | ||||
---|---|---|---|---|---|
STEEL GRADE | Carbon | Manganese | Silicon | Sulfur | Phosphorus |
Max % / Range | |||||
ASTM A27 / A27M | |||||
Grade N-1 | 0.25 | 0.75 | 0.80 | 0.06 | 0.05 |
Grade N-2 | 0.35 | 0.60 | 0.80 | 0.06 | 0.05 |
Grade U60-30 | 0.25 | 0.75 | 0.80 | 0.06 | 0.05 |
Grade 60-30 | 0.30 | 0.60 | 0.80 | 0.06 | 0.05 |
Grade 65-35 | 0.30 | 0.70 | 0.80 | 0.06 | 0.05 |
Grade 70-36 | 0.35 | 0.70 | 0.80 | 0.06 | 0.05 |
Grade 70-40 | 0.25 | 1.20 | 0.80 | 0.06 | 0.05 |
ASTM A148 / A148M | |||||
Grade 80-40 | N/A | N/A | N/A | 0.06 | 0.05 |
Grade 80-50 | N/A | N/A | N/A | 0.06 | 0.05 |
Grade 90-60 | N/A | N/A | N/A | 0.06 | 0.05 |
ASTM A216 / A216M | |||||
Grade WCA | 0.25 | 0.70 | 0.60 | 0.045 | 0.04 |
Grade WCB | 0.30 | 1.00 | 0.60 | 0.045 | 0.04 |
Grade WCC | 0.25 | 1.20 | 0.60 | 0.045 | 0.04 |
Cast Iron mechanical properties
ASTM | Mechanical Properties | |||
---|---|---|---|---|
STEEL GRADE | Tensile Strength | Yield Point | Elongation in 2 in. | Reduction of Area |
Min. ksi [Mpa] / Range | Min. % | |||
ASTM A27 / A27M | ||||
Grade U60-30 | 60 [415] | 30 [205] | 22 | 30 |
Grade 60-30 | 60 [415] | 30 [205] | 24 | 35 |
Grade 65-35 | 65 [450] | 35 [240] | 24 | 35 |
Grade 70-36 | 70 [485] | 36 [250] | 22 | 30 |
Grade 70-40 | 70 [485] | 40 [275] | 22 | 30 |
ASTM A148 / A148M | ||||
Grade 80-40 | 80 [550] | 40 [275] | 18 | 30 |
Grade 80-50 | 80 [550] | 50 [345] | 22 | 35 |
Grade 90-60 | 90 [620] | 60 [415] | 20 | 40 |
ASTM A216 / A216M | ||||
Grade WCA | 60-85 [415-585] | 30 [205] | 24 | 35 |
Grade WCB | 70-95 [485-655] | 36 [250] | 22 | 35 |
Grade WCC | 70-95 [485-655] | 40 [275] | 22 | 35 |
AISI 4140 Heat Treatment
Soft annealing °C | Cooling | Hardness HB |
---|---|---|
650-700 | slowly | max. 280 |
Stress-relief annealing °C | Cooling |
---|---|
630 – 650 | Furnace |
1st pre-heating °C | 2nd and 3rd | Hardening °C | Quenching | Tempering °C | Hardness after Teperature HRC |
---|---|---|---|---|---|
up to approx. 400 in an air-circulating furnace | 780 and 1000 | 1190 – 1230 | Saltbath, at least 520 °C Oil ,Air | at least twice 530-560 | 64 – 66 |
Wrought Iron chemical composition
Element | Iron, Fe | Carbon, C | Phosphorus, P | Silicon, Si | Sulfur, S | Manganese, Mn |
---|---|---|---|---|---|---|
Content (%) | 99-99.8 | 0.05-0.25 | 0.05-0.2 | 0.02-0.2 | 0.02-0.1 | 0.01-0.1 |
Wrought Steel mechanical properties
Properties | Imperial | Metric |
---|---|---|
Tensile strength | 34000-54000 psi | 234-372 MPa |
Modulus of elasticity | 28000 ksi | 193100 MPa |
Yield strength | 23000-32000 psi | 159-221 MPa |
Inspection and Testing of Cast steel
- Dimensional accuracy
- Surface finish condition
- Internal soundness
- Chemical analysis
- Heat analysis
- Tensile properties
- Impact properties
- Hardness
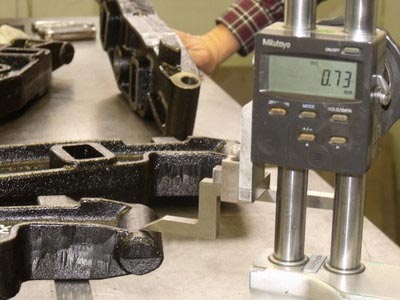
Manufacturing process of 4340 steel casting
- Furnace charging
- Melting
- Refining
- De-slagging
- Tapping (or tap out)
- Furnace turn-around
Refer cast steel valves uses and temperature limit
Cast steel valves temperature range
Temperature range | -29°C to 425°C |
---|
Difference between Wrought Iron and Steel
Characteristics | Wrought Iron | Steel |
---|---|---|
Carbon content | 0.08% | 4% |
Tensile Strength | Very good tensile strength | Greater tensile strength |
Workmanship | Requires less workmanship. | Requires more craftsmanship than wrought iron |
Surface finish of Cast iron parts
- Shot Blasting
- Painting
- Powder Coating
- Electroplating
Clear Plastic Box
It also called clear plastic folding packaging ,it widely used in supermarkets or shopping malls to display gift packaging ,such as candy biscuits for children,and surprise gifts on Christmas Day.It has two different types ,one is clear plastic box ,one is Plastic Print Box (plastic print box can print the logo according to customer requirements).It has a transparent appearance and can display the contents in it well.The assembly is quickly and easy,and transportation cost is also saved during transportationand storage .
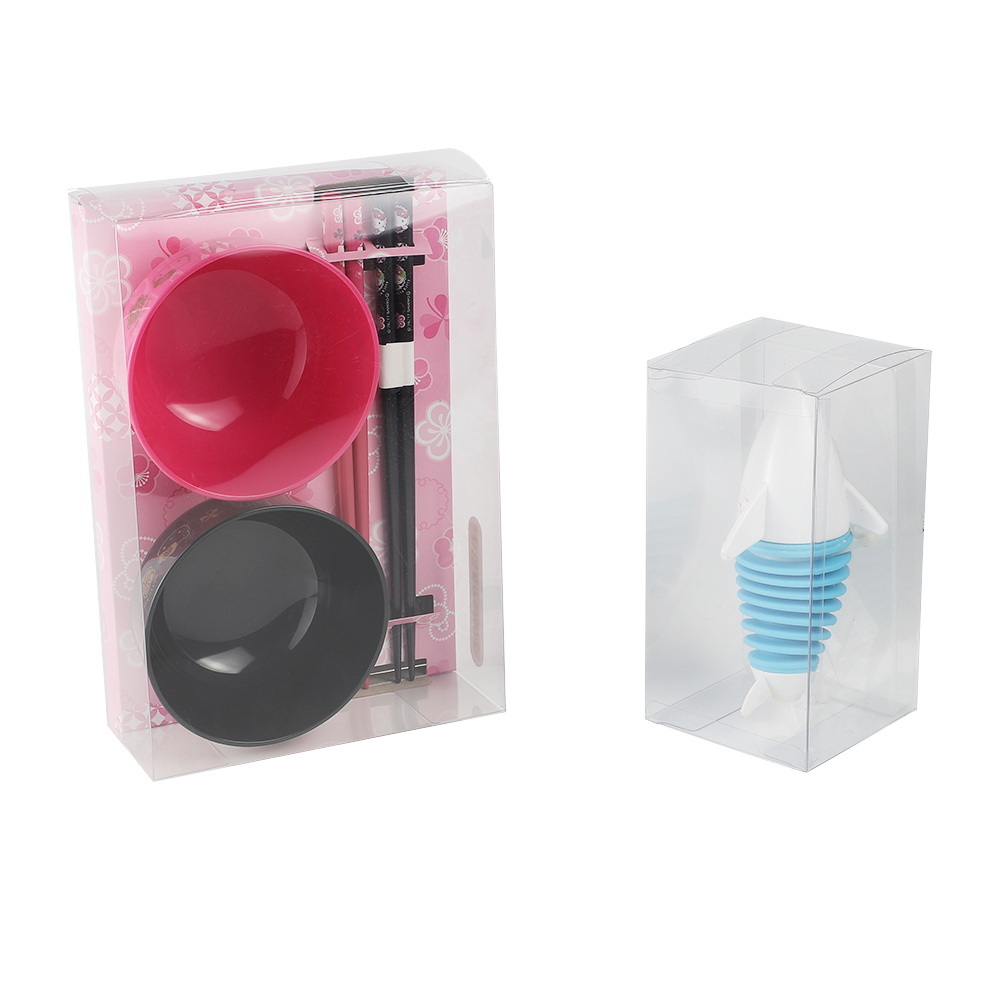
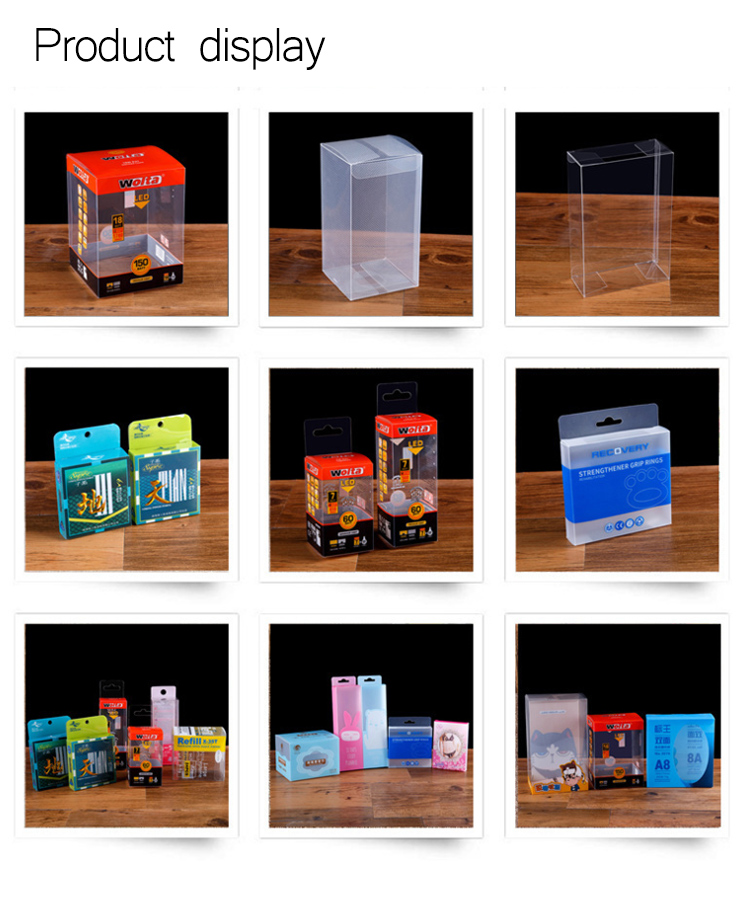
With tuck in tops and bottoms .Tuck top boxes have a tuck top plus two small side flaps on the top opening of the box along the top edges.Suitable for packaging small gifts & crafts,jewwlry,chocolate,speciality candy which can make a memorable surprise for your guests.Can be decorated with colored ribbon ,flowers or afix to personalized labels ,stickers or charms to match your weddin theme.
Clear Pvc Box,Clear Plastic Box,Acetate Gift Box,Clear Plastic Pillow Box
Shenzhen Stardeal Industrial Co.,Ltd , https://www.plasticblisterpack.com