When it comes to special vehicles, we have to think of its own special equipment. It is precisely because of this that special vehicles have become the indispensable equipment for transportation and special operations in the national economy. The chassis is the basic part of the special-purpose vehicle, and it is also the relative core part. It plays a crucial role in the special performance and role of the special-purpose vehicle.
The composition of the chassis
The basic composition of the chassis is relatively simple, generally including the drive train, driving train, steering train and brake train. However, the functions and mutual cooperation of each part are more complicated, and the follow-up will gradually be opened for everyone.
Chassis classification
The classification of the chassis is mainly based on the classification of special-purpose vehicles. According to the provisions in GB/T17350-2009, the classification of special-purpose vehicles can be divided into the following categories:
Conventional vans, tank trucks, and special dump trucks are usually designed to use the chassis of the second class vehicle; passenger cars, passenger cars, vans, and vans usually use three types of chassis modifications.
The specific classification of the chassis is as follows: Class 1, Class 2, Class 3 and Class 4 chassis.
One type of chassis is the vehicle in the usual sense, including the entire system of the car.
The second type of chassis lacks a car system assembly, but it has a driving area, a front instrument, an operating system, etc., and can normally travel. Most special vehicles require the installation of special tools. Therefore, the second type of chassis provides a natural basis for special vehicles and becomes the most used type of chassis for special vehicles.
The three types of chassis have no body, but they have an engine, a transmission, a front and rear axle, a steering gear, a suspension device, a wheel, a brake system, etc., and cannot be used.
There are no forming parts in the four types of chassis, which are basically parts of the entire chassis system of the car.
In fact, one to four types of chassis can also be referred to as one type of automobile, two types of automobiles, three types of automobiles, and four types of automobiles. In the field of special vehicles, the concept of chassis is used more often.
The name of the chassis
The naming rules of the chassis are similar to those of the domestic automobile model, and are divided into the head section, the middle section and the tail section, and the rules of each section are basically the same. Take the "Chusheng Brand CSC5256GJBS Concrete Mixer" as an example, the chassis model of "Shaanxi SX5256GJBDR404" is used. It can be seen from the comparison that apart from the company name code of the first company and the company's self-definition code at the tail, "5256GJB "This part of the special car information has the same code. If necessary, please refer to http://news.chinacar.com.cn/newsview113644.html .
Chassis related company code as shown:
Chassis drive form
The driving mode of the chassis largely determines the passing capacity of the vehicle. The more drives, the stronger the passing capacity of the vehicle, but the more complex the structure, the higher the quality of the trimming and the corresponding increase in the manufacturing cost.
At present, there are 4*2, 4*4, 6*2, 6*4, 6*6, 8*4, 8*8, 10*4 and so on. The previous figure represents the total number of car wheels. A single digit indicates the number of drive wheels. According to the requirements of special purpose vehicles, quality, etc., we can choose the appropriate drive form, generally 4*2 drive form, simple structure, low manufacturing cost, and wider application.
As a basic component of a car, the structure of the chassis is relatively complex, and the knowledge principles used are numerous and inconvenient. This time we have a basic understanding of the classification, naming and driving forms of the chassis. I believe that with the continuous deepening of understanding We will all have a new understanding of the chassis.
Sintering Parts:
There are similarities with the production of ceramic powder sintering technology, are, therefore, a series of powder metallurgy new technology can also be used in the preparation of ceramic materials. Because of the advantages of powder metallurgical technology, it has become the key problem to solve new materials, plays an important role in the development of new materials in powder metallurgy products. Including milling and milling which is mainly metallurgical process, and powder metallurgy products and literal agreement. It is often far beyond the category of materials and metallurgy, often across multiple studies (materials and metallurgy, machinery and Mechanical) technology. Especially the modern printing metal powder 3D, in Mechanical Engineering Cheng, CAD, reverse engineering technology, layered manufacturing technology, numerical control technology, materials science, laser technology, makes the product technology of powder metallurgy technology has become a modern comprehensive more cross discipline.
Based on different raw material,we can make Carbon Steel Sintering and Stainless Steel Sintering parts.
Advantages:
Powder metallurgy has unique chemical composition and mechanical, physical properties, and these properties can not be obtained by traditional casting method. Be made directly using porous powder metallurgy technology, semi dense or fully dense materials and products, such as oil bearing, gear, cam, a guide rod, a cutter.
(1) The process of powder metallurgy technology can minimize alloy composition segregation, eliminate thick, uneven casting organization. In the preparation of high performance rare earth permanent magnetic materials, rare earth hydrogen storage materials, rare earth luminescent materials, rare earth catalyst, high temperature superconducting materials, new metal materials (such as Al-Li alloy, heat-resistant al super alloy, alloy powder, corrosion resistance of stainless steel, high-speed steel powder, intermetallic compound high temperature structural materials) plays an important role.
(2) It can be prepared by amorphous, microcrystalline, quasicrystals, nanocrystalline and supersaturated solid solution of a series of high performance etc. The balance of materials, these materials have excellent electrical, magnetic, optical and mechanical properties.
(3) It can be easily combined with various types, give full play to the characteristics of each element of the respective materials, is a kind of high performance metal based ceramic composite material and low cost technology.
(4) It can make special structure and properties of the production that ordinary smelting method can`t produce, such as a new type of porous biomaterials, porous membrane material, structure and function of high performance ceramic abrasive material.
(5) It can realize near net forming and automatic batch production, which can effectively reduce the production of resources and energy consumption
(6) It can make full use of ore tailings, steelmaking sludge, mill scale, scrap metal recycling as raw materials, is a kind of new technology can be effective and comprehensive utilization of renewable materials.
Manufacturing process:
(1) The production of powder. It includes powder preparation, mixing and other steps. For powder molding and plasticity improve powder usually add oil, rubber or paraffin as plasticizer.
(2) Pressing powder. Under the pressure of 15-600mpa, pressed into the desired shape;
(3) High temperature sintering furnace or vacuum furnace. In a protective atmosphere in sintering. Unlike metal melting, sintering at least one element is in solid state. The sintering process of powder particles by diffusion, recrystallization, welding, chemical, physical and chemical dissolution process of a series, as metallurgy products have a certain porosity.
(4) Postprocessing. In general, good Sintering Parts can be used directly. But for some high precision size requirements and has high hardness and wear resistance of the parts but also for sintering postprocessing. Postprocessing including precision pressing, rolling, extrusion, quenching, quenching, oil, And infiltration, etc.
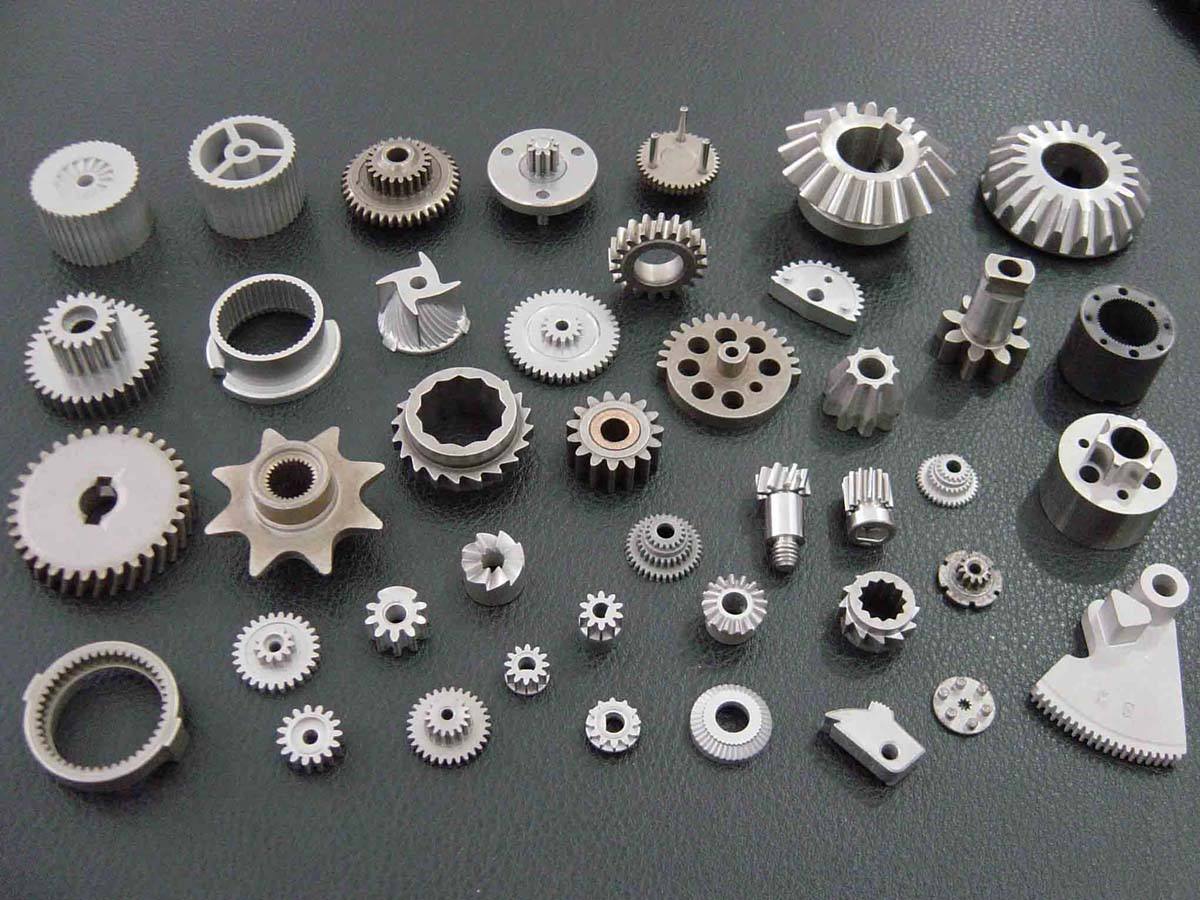
Sintering Parts
Sintering Parts,Carbon Steel Sintering,Stainless Steel Sintering,High Performance Sintering Parts
VESTA Motoring Ltd , https://www.vesta-industry.com