Back To Blog
The Benefits of Waterjet Cutting Services
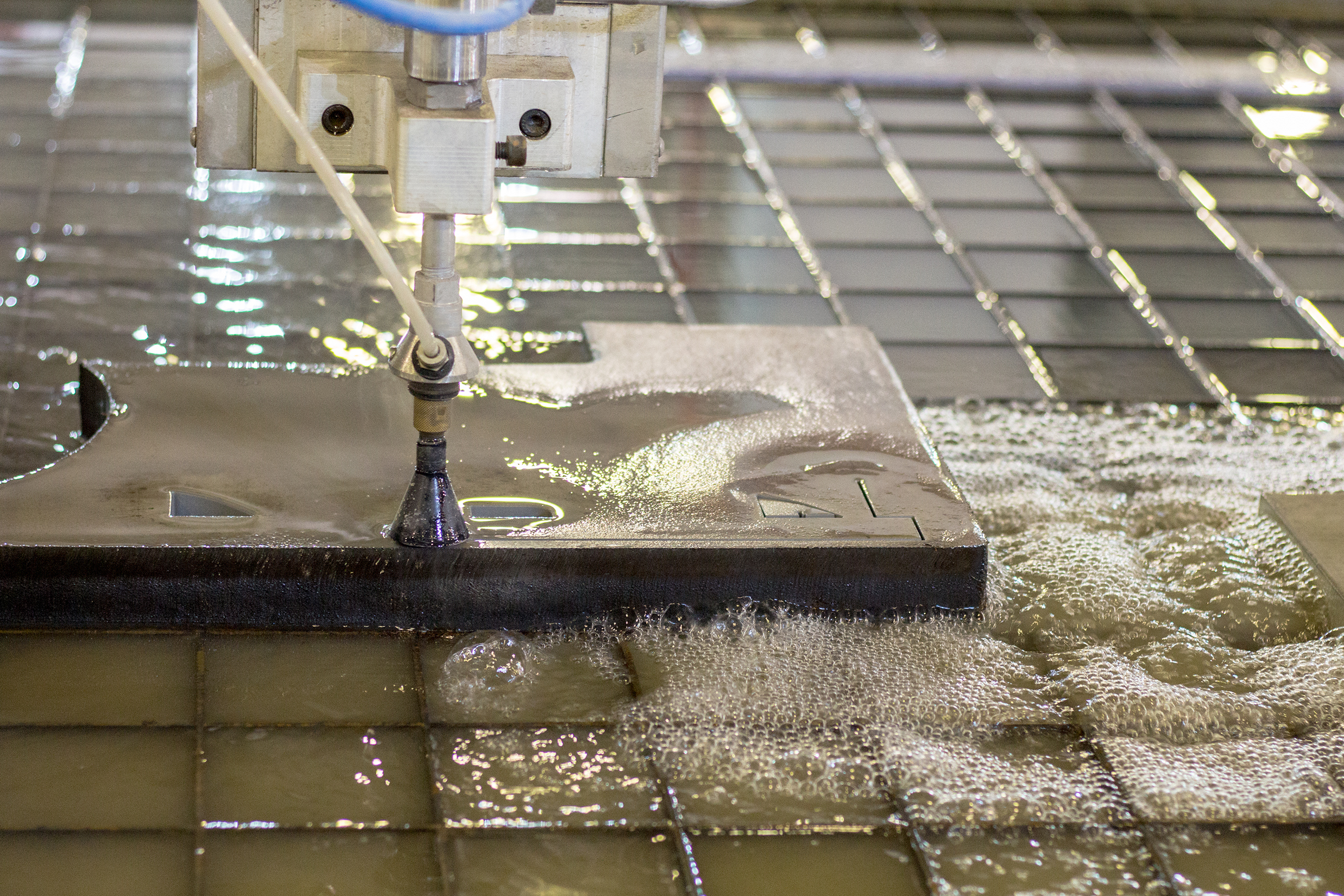
Waterjet cutting is a powerful and flexible method that delivers exceptional precision, no matter the material or application. Whether you're working with metals, stone, glass, foam, or composites like fiberglass and carbon fiber, waterjet technology can handle it all with ease.
This advanced cutting technique is known for its ability to produce clean, sharp edges without any heat distortion. It's ideal for intricate designs, whether you're slicing through thick steel or delicate glass. The result? Perfect cuts every time, with no rough edges or extra finishing required.
Whether you're in aerospace, automotive, or architectural design, waterjet cutting can help bring your ideas to life. Discover how this precision technology can improve your manufacturing process and take your projects to the next level.
What Is Waterjet Cutting?
Waterjet cutting uses a high-pressure stream of water mixed with abrasive materials such as garnet, zirconia, or silicon carbide to cut through a wide range of materials. It’s especially useful for creating complex shapes and cutting materials that are challenging with traditional methods like sawing or drilling.
When speed, accuracy, and flexibility are essential, waterjet cutting provides reliable and consistent results that meet even the most demanding standards.
Advantages of Waterjet Cutting
Waterjet cutting offers a unique combination of versatility and precision, making it a top choice across many industries. Some of its key benefits include:
Precision Cutting
With unmatched accuracy, waterjet cutting allows for highly detailed and intricate designs that other methods often struggle to achieve. Whether cutting metal, stone, or delicate materials, waterjets deliver exact shapes with tight tolerances. This precision also reduces the need for costly secondary finishing processes.
Versatility With Various Materials
One of the greatest strengths of waterjet cutting is its ability to work with almost any material, from soft foams to hard metals and ceramics. This makes it an excellent choice for industries like aerospace, automotive, and architecture, where complex and precise cuts are essential.
No Heat-Affected Zones
Unlike laser or plasma cutting, waterjet cutting doesn’t generate heat during the process. This means there are no heat-affected zones (HAZ) that could alter the material’s properties. For materials like aluminum and steel, this helps maintain their original strength and structural integrity.
Superior Edge Quality
Waterjet cutting produces smooth, clean edges that require minimal additional finishing. This is particularly valuable in applications where aesthetics and precision are important, such as decorative metalwork or architectural installations.
No Thickness Limitation
Waterjet cutting can handle materials up to 6 inches thick, making it suitable for both thin sheets and thick slabs of stone, glass, or metal. This flexibility makes it ideal for large-scale industrial projects and detailed, custom work alike.
Multi-Axis Cutting
Modern waterjet machines support multi-axis cutting, allowing for complex 3D shapes and angles. This capability is especially beneficial for industries like aerospace, where intricate geometries are common and traditional two-dimensional cuts fall short.
Environmentally Friendly
Waterjet cutting is a clean and efficient process that uses only water and an abrasive material. Unlike other cutting methods, it doesn't produce harmful fumes, dust, or pollutants. This makes it a great option for companies focused on sustainability and reducing their environmental impact.
How Waterjet Cutting Enhances Manufacturing Efficiency
By enabling fast and accurate cutting of complex shapes, waterjet technology helps manufacturers reduce production time and minimize waste. It ensures consistent quality across different materials and applications, making it a valuable tool for improving overall efficiency in the manufacturing process.
Choose Sur-Seal for Reliable Waterjet Cutting Services
Since 1940, Sur-Seal has been committed to delivering innovative solutions that help manufacturers succeed. Our expert team specializes in waterjet cutting and provides top-quality results for even the most challenging projects.
Let’s collaborate to bring your vision to life with precision, efficiency, and excellence.
CPE Laminate Nonwoven Fabric Machine
Casting machine refers to the best equipment for making cast film. Adopt high-precision electronic ceramic casting machine and use alumina as the main raw material for ceramic casting
First, mix the pulverized powder with binder, plasticizer, dispersant, and solvent to make a slurry with a certain viscosity. The slurry flows down from the hopper and is
The scraper is scraped and coated on the solid base tape with a certain thickness, and after drying and curing, the film that becomes the green tape is peeled off from the top, and then according to the size of the finished product
Dimensions and shapes require punching, lamination, and other processing of the green belt to make a finished blank to be sintered. Low cost, high quality, non-toxic
Harmless, simple production process and other advantages
Cpe Laminate Nonwoven Fabric Machine,Flat Film Plastic Tape Extrusion Machine,Hygienic Packing Film Machine,Cpe Nonwoven Fabric Machine
Baijia Mechanical Equipment (Huizhou) Co., Ltd. , https://www.castfilmmachine.com